Destylator przemysłowy to urządzenie, które wykorzystuje proces destylacji do oddzielania substancji na podstawie różnicy w temperaturze wrzenia. W praktyce oznacza to, że surowe materiały, takie jak woda, alkohol czy oleje, są podgrzewane do momentu, gdy zaczynają parować. Para następnie przemieszcza się do chłodnicy, gdzie schładza się i skrapla z powrotem do cieczy. Proces ten jest kluczowy w wielu branżach, takich jak przemysł chemiczny, farmaceutyczny czy spożywczy. W zależności od zastosowania, destylatory mogą być zaprojektowane na różne sposoby, aby osiągnąć pożądany poziom czystości produktu końcowego. Na przykład w produkcji alkoholu ważne jest, aby oddzielić etanol od innych składników, co wymaga precyzyjnego ustawienia temperatury i ciśnienia. W przemyśle chemicznym destylatory są często używane do separacji różnych frakcji chemicznych, co pozwala na uzyskanie czystych substancji wykorzystywanych w dalszych procesach produkcyjnych.
Jakie są rodzaje destylatorów przemysłowych dostępnych na rynku
Na rynku dostępnych jest wiele różnych typów destylatorów przemysłowych, które różnią się konstrukcją oraz zastosowaniem. Jednym z najpopularniejszych rodzajów jest destylator prosty, który składa się z jednego kolumny i jest stosunkowo łatwy w obsłudze. Tego typu urządzenia są często wykorzystywane w małych zakładach produkcyjnych oraz laboratoriach. Kolejnym rodzajem są destylatory frakcyjne, które mają bardziej skomplikowaną budowę i pozwalają na oddzielanie wielu frakcji jednocześnie. Dzięki zastosowaniu kolumny frakcyjnej możliwe jest uzyskanie wyższej czystości produktów końcowych. W przemyśle petrochemicznym często wykorzystuje się także destylatory próżniowe, które działają w obniżonym ciśnieniu. Dzięki temu można destylować substancje o wysokiej temperaturze wrzenia bez ryzyka ich rozkładu. Istnieją również destylatory azeotropowe, które są używane do separacji mieszanin trudnych do rozdzielenia ze względu na tworzenie azeotropów.
Jakie są zalety stosowania destylatorów przemysłowych
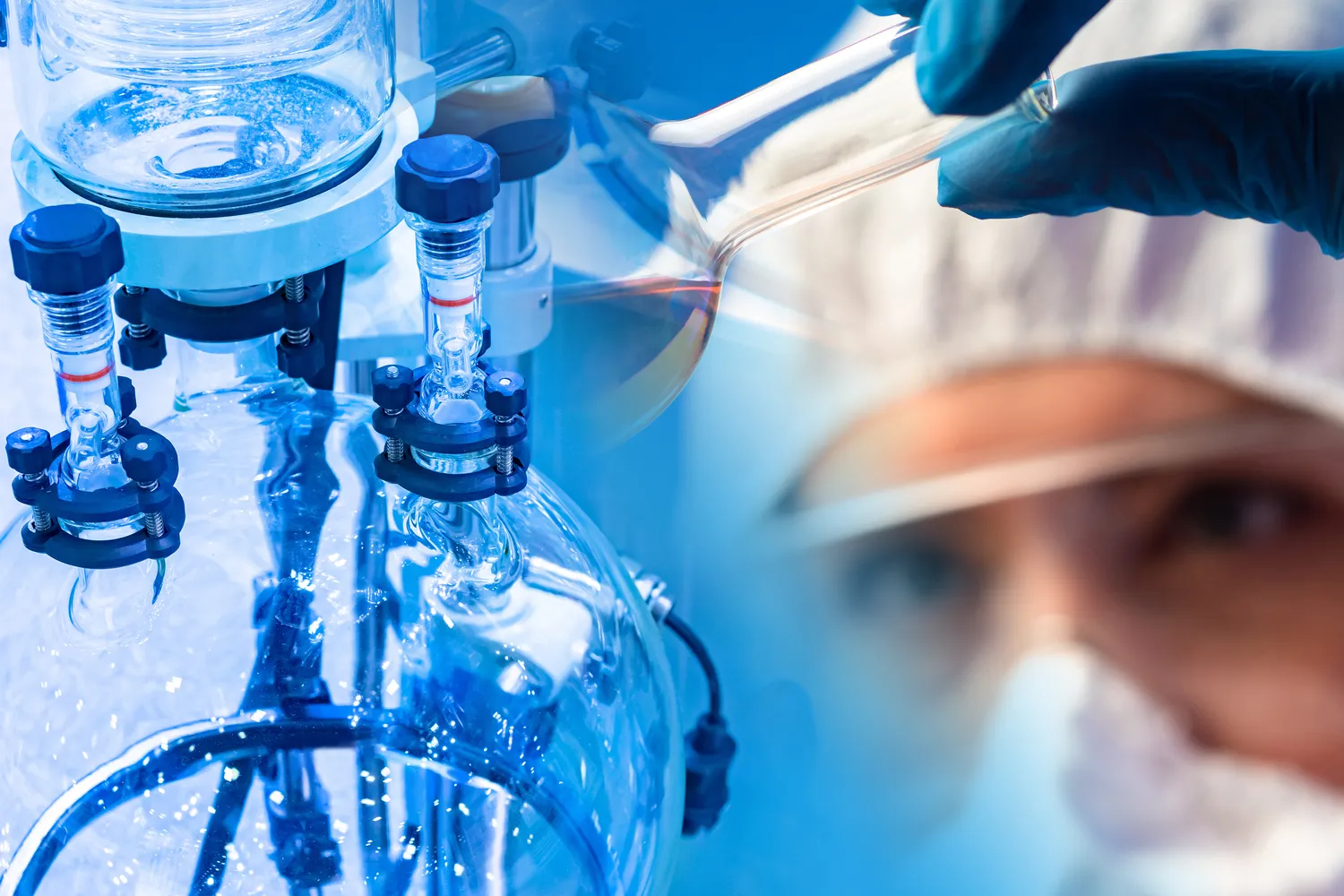
Stosowanie destylatorów przemysłowych niesie ze sobą wiele korzyści zarówno dla producentów, jak i dla konsumentów. Przede wszystkim umożliwiają one uzyskanie wysokiej jakości produktów poprzez skuteczne oddzielanie niepożądanych substancji oraz zanieczyszczeń. Dzięki temu finalne produkty charakteryzują się lepszymi właściwościami chemicznymi oraz fizycznymi, co ma kluczowe znaczenie w branży farmaceutycznej czy spożywczej. Ponadto nowoczesne destylatory są zaprojektowane tak, aby były energooszczędne i wydajne, co przekłada się na niższe koszty produkcji. Wiele z nich wyposażonych jest w zaawansowane systemy automatyzacji, co pozwala na monitorowanie i kontrolowanie procesu w czasie rzeczywistym. To z kolei minimalizuje ryzyko błędów ludzkich oraz zwiększa bezpieczeństwo pracy. Dodatkowo stosowanie destylatorów przemysłowych przyczynia się do ochrony środowiska poprzez redukcję odpadów oraz emisji szkodliwych substancji do atmosfery.
Jakie zastosowania mają destylatory przemysłowe w różnych branżach
Destylatory przemysłowe znajdują szerokie zastosowanie w wielu branżach gospodarki, co czyni je niezwykle uniwersalnymi urządzeniami. W przemyśle chemicznym służą do separacji różnych frakcji chemicznych oraz oczyszczania surowców przed dalszym przetwarzaniem. W branży farmaceutycznej są wykorzystywane do produkcji leków oraz substancji czynnych o wysokiej czystości. Destylatory odgrywają również kluczową rolę w przemyśle spożywczym, gdzie służą do produkcji alkoholu oraz ekstraktów roślinnych. W przypadku produkcji napojów alkoholowych proces destylacji pozwala na uzyskanie pożądanej mocy trunku oraz jego aromatu poprzez selektywne oddzielanie składników smakowych i zapachowych. W przemyśle petrochemicznym natomiast stosuje się je do rafinacji ropy naftowej oraz produkcji paliw płynnych poprzez separację poszczególnych frakcji olejowych. Oprócz tego destylatory znajdują zastosowanie w laboratoriach badawczych, gdzie służą do analizy chemicznej oraz syntez chemicznych.
Jakie są kluczowe elementy konstrukcyjne destylatora przemysłowego
Destylator przemysłowy składa się z kilku kluczowych elementów konstrukcyjnych, które współpracują ze sobą, aby zapewnić efektywny proces destylacji. Podstawowym komponentem jest zbiornik, w którym umieszczany jest surowiec do destylacji. Zbiornik ten jest często wyposażony w system grzewczy, który podgrzewa ciecz do momentu jej wrzenia. Kolejnym istotnym elementem jest kolumna destylacyjna, która pełni funkcję separacyjną. W kolumnie tej zachodzi proces frakcjonowania, w którym para przemieszcza się w górę kolumny, a ciecz opada w dół. W zależności od konstrukcji kolumny mogą być zastosowane różne media, takie jak sita czy pierścienie, które zwiększają powierzchnię kontaktu między parą a cieczą, co poprawia efektywność separacji. Po przejściu przez kolumnę para trafia do chłodnicy, gdzie schładza się i skrapla z powrotem do cieczy. Chłodnica może mieć różne formy, w tym chłodnice rurowe lub płytowe, a ich wybór zależy od specyfiki procesu. Ostatnim kluczowym elementem jest zbiornik odbiorczy, w którym gromadzi się produkt końcowy.
Jakie czynniki wpływają na efektywność destylacji przemysłowej
Efektywność destylacji przemysłowej zależy od wielu czynników, które mogą wpływać na jakość oraz ilość uzyskiwanego produktu końcowego. Jednym z najważniejszych aspektów jest temperatura wrzenia substancji, która determinuje moment rozpoczęcia procesu parowania. Precyzyjne kontrolowanie temperatury jest kluczowe dla uzyskania pożądanej czystości frakcji. Również ciśnienie odgrywa istotną rolę – obniżenie ciśnienia może pozwolić na destylację substancji o wysokiej temperaturze wrzenia bez ich rozkładu. Kolejnym czynnikiem jest czas trwania procesu destylacji; zbyt krótki czas może prowadzić do niedostatecznego oddzielenia frakcji, podczas gdy zbyt długi czas może skutkować utratą cennych składników. Ważne jest również odpowiednie dobranie mediów w kolumnie destylacyjnej, które zwiększają powierzchnię kontaktu między parą a cieczą. Dodatkowo jakość surowca wyjściowego ma ogromny wpływ na efektywność procesu – im czystszy surowiec, tym łatwiejsze osiągnięcie wysokiej jakości produktu końcowego.
Jakie są najnowsze technologie w dziedzinie destylacji przemysłowej
W ostatnich latach nastąpił znaczący rozwój technologii związanych z destylacją przemysłową, co przyczyniło się do zwiększenia efektywności oraz jakości procesów produkcyjnych. Jednym z najważniejszych trendów jest automatyzacja procesów destylacyjnych, która pozwala na precyzyjne monitorowanie i kontrolowanie warunków pracy urządzeń. Dzięki zastosowaniu zaawansowanych systemów czujników oraz oprogramowania możliwe jest dostosowanie parametrów pracy w czasie rzeczywistym, co minimalizuje ryzyko błędów ludzkich i zwiększa bezpieczeństwo operacji. Innym nowoczesnym rozwiązaniem są destylatory membranowe, które wykorzystują membrany do separacji składników na poziomie molekularnym. Ta technologia pozwala na osiągnięcie wyższej czystości produktów oraz zmniejszenie zużycia energii w porównaniu do tradycyjnych metod destylacyjnych. Ponadto rozwijane są także technologie odzysku ciepła oraz systemy recyklingu rozpuszczalników, które przyczyniają się do zmniejszenia wpływu na środowisko oraz obniżenia kosztów produkcji. Wprowadzenie innowacyjnych materiałów budowlanych i konstrukcyjnych również wpłynęło na poprawę wydajności i trwałości urządzeń destylacyjnych.
Jakie są wyzwania związane z eksploatacją destylatorów przemysłowych
Eksploatacja destylatorów przemysłowych wiąże się z wieloma wyzwaniami, które mogą wpływać na ich wydajność oraz bezpieczeństwo pracy. Jednym z głównych problemów jest konieczność regularnego czyszczenia urządzeń, ponieważ osady i zanieczyszczenia mogą prowadzić do obniżenia efektywności procesu oraz jakości produktu końcowego. Zanieczyszczenia te mogą pochodzić zarówno z surowców używanych do destylacji, jak i z samego procesu technologicznego. Kolejnym wyzwaniem jest zarządzanie zużyciem energii; procesy destylacyjne często wymagają dużych ilości energii cieplnej, co może generować wysokie koszty operacyjne oraz negatywnie wpływać na środowisko. Dodatkowo operatorzy muszą być odpowiednio przeszkoleni w zakresie obsługi urządzeń oraz monitorowania warunków pracy, aby uniknąć potencjalnych awarii czy niebezpieczeństw związanych z pracą z substancjami chemicznymi.
Jakie są przyszłe kierunki rozwoju technologii destylacji przemysłowej
Przyszłość technologii destylacji przemysłowej rysuje się w jasnych barwach dzięki ciągłemu postępowi technologicznemu oraz rosnącym wymaganiom rynku dotyczących jakości produktów i ochrony środowiska. Jednym z głównych kierunków rozwoju jest zwiększenie efektywności energetycznej procesów destylacyjnych poprzez wdrażanie innowacyjnych rozwiązań takich jak odzysk ciepła czy zastosowanie alternatywnych źródeł energii odnawialnej. Ponadto rozwój technologii cyfrowych i automatyzacji będzie miał kluczowe znaczenie dla optymalizacji procesów produkcyjnych; inteligentne systemy monitorowania będą pozwalały na bieżąco analizować dane i dostosowywać parametry pracy urządzeń w celu maksymalizacji wydajności i minimalizacji strat surowców. W kontekście ochrony środowiska coraz większą uwagę zwraca się także na rozwój technologii zielonej chemii oraz bardziej ekologicznych metod separacji substancji chemicznych. W przyszłości możemy również spodziewać się większego nacisku na recykling i ponowne wykorzystanie rozpuszczalników oraz innych materiałów wykorzystywanych w procesach destylacyjnych.