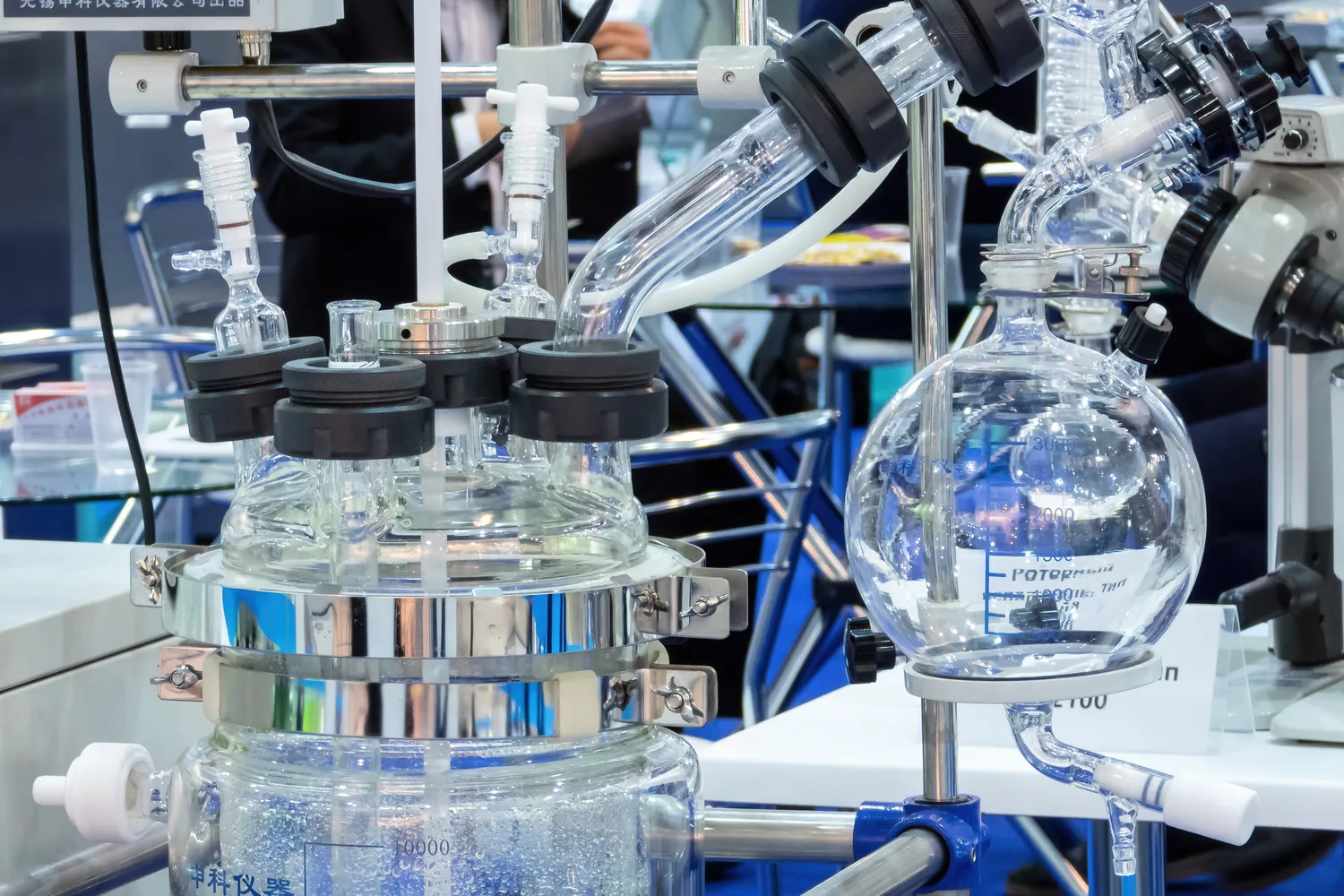
Destylacja rozpuszczalników to proces, który polega na oddzieleniu składników mieszaniny na podstawie różnicy w ich temperaturach wrzenia. W praktyce oznacza to, że ciecz, która ma niższą temperaturę wrzenia, odparowuje jako pierwsza, a następnie skrapla się w chłodnicy, tworząc czystszy produkt. Proces ten jest szeroko stosowany w przemyśle chemicznym oraz farmaceutycznym do oczyszczania i odzyskiwania rozpuszczalników. W destylacji rozpuszczalników kluczowe znaczenie ma dobór odpowiednich warunków, takich jak temperatura i ciśnienie, które wpływają na efektywność procesu. Istnieją różne metody destylacji, w tym destylacja prosta, frakcyjna oraz podciśnieniowa. Każda z tych metod ma swoje zastosowanie w zależności od charakterystyki rozpuszczalników oraz pożądanej czystości końcowego produktu. Warto również zaznaczyć, że destylacja nie tylko pozwala na oczyszczanie substancji, ale także na ich separację w celu dalszego wykorzystania.
Jakie są zastosowania destylacji rozpuszczalników w przemyśle
Zastosowania destylacji rozpuszczalników w przemyśle są niezwykle różnorodne i obejmują wiele dziedzin. W przemyśle chemicznym destylacja jest kluczowym procesem wykorzystywanym do oczyszczania surowców oraz produkcji gotowych produktów chemicznych. Na przykład, w produkcji alkoholi etylowych destylacja pozwala na oddzielenie czystego alkoholu od innych składników fermentacyjnych. W branży farmaceutycznej proces ten jest niezbędny do uzyskania czystych substancji czynnych wykorzystywanych w lekach. Ponadto, w przemyśle petrochemicznym destylacja frakcyjna jest stosowana do separacji różnych frakcji ropy naftowej, co umożliwia produkcję benzyny, oleju napędowego oraz innych paliw. Destylacja znajduje również zastosowanie w recyklingu rozpuszczalników organicznych, co przyczynia się do ochrony środowiska poprzez zmniejszenie ilości odpadów chemicznych.
Jakie są najważniejsze rodzaje destylacji rozpuszczalników
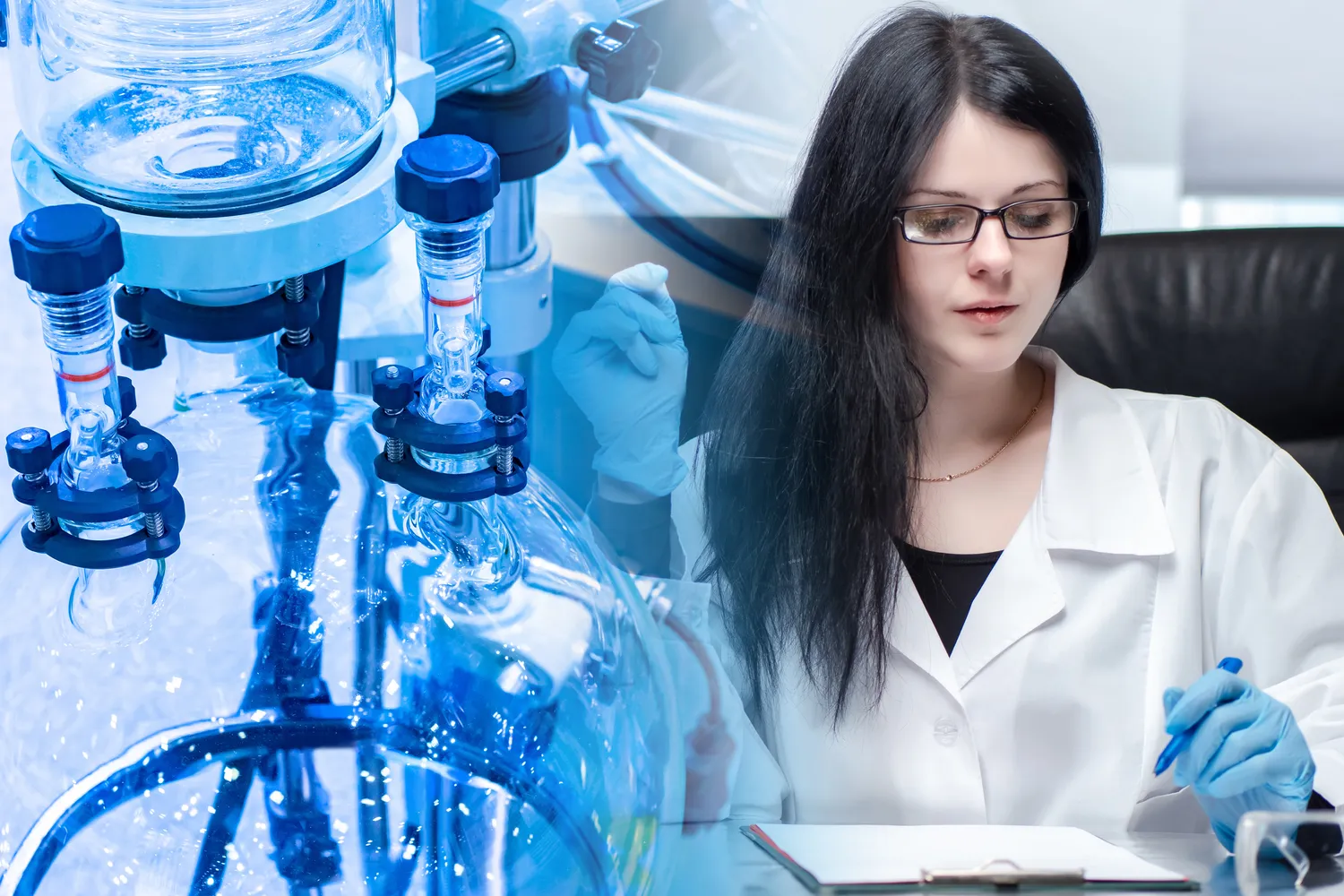
W kontekście destylacji rozpuszczalników wyróżnia się kilka kluczowych rodzajów tego procesu, z których każdy ma swoje specyficzne zastosowanie i zalety. Destylacja prosta to najstarsza i najczęściej stosowana metoda, która polega na jednorazowym odparowaniu cieczy i skropleniu pary. Jest ona idealna do separacji substancji o znacznej różnicy temperatur wrzenia. Z kolei destylacja frakcyjna jest bardziej zaawansowaną techniką, która umożliwia separację mieszanin zawierających kilka składników o zbliżonych temperaturach wrzenia. Dzięki zastosowaniu kolumny frakcyjnej możliwe jest uzyskanie wyższej czystości produktów końcowych. Innym rodzajem jest destylacja podciśnieniowa, która odbywa się w obniżonym ciśnieniu atmosferycznym. Ta metoda pozwala na obniżenie temperatury wrzenia substancji, co jest szczególnie istotne dla termolabilnych związków chemicznych. Warto również wspomnieć o destylacji azeotropowej, która jest stosowana do separacji mieszanin azeotropowych poprzez dodanie odpowiednich reagentów.
Jakie są korzyści płynące z użycia destylacji rozpuszczalników
Korzyści płynące z użycia destylacji rozpuszczalników są liczne i znaczące zarówno dla przemysłu, jak i dla ochrony środowiska. Przede wszystkim proces ten pozwala na uzyskanie wysokiej czystości substancji chemicznych, co jest kluczowe w wielu aplikacjach przemysłowych oraz badawczych. Czyste rozpuszczalniki są niezbędne do produkcji leków, kosmetyków czy materiałów budowlanych, gdzie jakość surowców ma bezpośredni wpływ na bezpieczeństwo i skuteczność końcowych produktów. Ponadto destylacja umożliwia efektywne odzyskiwanie cennych substancji z odpadów przemysłowych, co przyczynia się do zmniejszenia kosztów produkcji oraz ograniczenia negatywnego wpływu na środowisko naturalne. Dzięki nowoczesnym technologiom możliwe jest także zwiększenie wydajności procesu oraz redukcja zużycia energii, co przekłada się na niższe koszty operacyjne zakładów przemysłowych.
Jakie są najczęstsze problemy związane z destylacją rozpuszczalników
Podczas procesu destylacji rozpuszczalników mogą wystąpić różne problemy, które wpływają na efektywność oraz jakość uzyskiwanych produktów. Jednym z najczęstszych wyzwań jest pojawienie się tzw. azeotropów, czyli mieszanin, które mają stały skład i nie można ich oddzielić za pomocą standardowej destylacji. Azeotropy mogą znacząco utrudnić proces separacji, co wymaga zastosowania dodatkowych metod, takich jak destylacja azeotropowa czy dodanie substancji pomocniczych. Innym problemem jest zanieczyszczenie surowców, które może prowadzić do obniżenia jakości końcowego produktu. Zanieczyszczenia mogą pochodzić zarówno z surowców wyjściowych, jak i z samego procesu destylacji, dlatego kluczowe jest monitorowanie jakości używanych materiałów oraz odpowiednie czyszczenie aparatury. Dodatkowo, niewłaściwe ustawienia parametrów procesu, takich jak temperatura czy ciśnienie, mogą prowadzić do nieefektywnej separacji składników. W przypadku destylacji frakcyjnej ważne jest także dobranie odpowiedniej kolumny frakcyjnej oraz jej parametrów operacyjnych, aby uzyskać optymalne wyniki.
Jakie są różnice między destylacją prostą a frakcyjną
Destylacja prosta i frakcyjna to dwie podstawowe metody stosowane w procesach separacji cieczy, które różnią się zarówno zasadą działania, jak i zastosowaniem. Destylacja prosta jest najprostszą formą tego procesu i polega na jednorazowym odparowaniu cieczy oraz skropleniu pary w chłodnicy. Jest ona skuteczna w przypadku mieszanin zawierających składniki o znacznej różnicy temperatur wrzenia, co pozwala na łatwe oddzielenie jednego składnika od drugiego. Z kolei destylacja frakcyjna jest bardziej skomplikowaną metodą, która umożliwia separację mieszanin o zbliżonych temperaturach wrzenia. W tym przypadku wykorzystuje się kolumnę frakcyjną, która zwiększa powierzchnię kontaktu między parą a cieczą, co pozwala na wielokrotne skraplanie i odparowywanie składników. Dzięki temu możliwe jest uzyskanie wyższej czystości produktów końcowych. W praktyce destylacja frakcyjna znajduje zastosowanie w przemyśle petrochemicznym do separacji różnych frakcji ropy naftowej oraz w produkcji alkoholi wysokoprocentowych.
Jakie są koszty związane z procesem destylacji rozpuszczalników
Koszty związane z procesem destylacji rozpuszczalników mogą być znaczne i zależą od wielu czynników, takich jak rodzaj używanej technologii, skala produkcji oraz jakość surowców. Na początku warto zwrócić uwagę na koszty inwestycyjne związane z zakupem odpowiednich urządzeń i aparatury do przeprowadzenia procesu destylacji. W przypadku dużych zakładów przemysłowych konieczne może być zainwestowanie w zaawansowane systemy destylacyjne, takie jak kolumny frakcyjne czy systemy podciśnieniowe, co wiąże się z wysokimi wydatkami początkowymi. Kolejnym istotnym elementem kosztów są wydatki operacyjne związane z zużyciem energii potrzebnej do podgrzewania cieczy oraz chłodzenia pary podczas procesu skraplania. Warto również uwzględnić koszty związane z utrzymaniem aparatury oraz ewentualnymi naprawami czy modernizacjami systemu. Koszty surowców również mają znaczenie – im wyższa jakość używanych materiałów, tym większe wydatki na ich zakup.
Jakie są nowoczesne technologie wykorzystywane w destylacji rozpuszczalników
Nowoczesne technologie wykorzystywane w destylacji rozpuszczalników stale ewoluują i dostosowują się do potrzeb przemysłu chemicznego oraz farmaceutycznego. Jednym z przykładów innowacyjnych rozwiązań jest zastosowanie technologii membranowych, które pozwalają na separację składników bez konieczności podgrzewania cieczy. Proces ten jest bardziej energooszczędny i może prowadzić do mniejszych strat cennych substancji chemicznych. Innym kierunkiem rozwoju są systemy automatyzacji i monitorowania procesów destylacyjnych, które umożliwiają precyzyjne kontrolowanie parametrów operacyjnych oraz zwiększenie efektywności produkcji. Dzięki zastosowaniu nowoczesnych czujników oraz oprogramowania możliwe jest szybkie reagowanie na zmiany warunków pracy oraz optymalizacja procesu w czasie rzeczywistym. Warto również wspomnieć o rozwijających się technologiach odzysku ciepła, które pozwalają na ponowne wykorzystanie energii generowanej podczas procesu destylacji, co przyczynia się do obniżenia kosztów operacyjnych oraz zmniejszenia wpływu na środowisko naturalne.
Jakie są najlepsze praktyki przy przeprowadzaniu destylacji rozpuszczalników
Przy przeprowadzaniu destylacji rozpuszczalników istnieje szereg najlepszych praktyk, które mogą znacząco wpłynąć na efektywność procesu oraz jakość uzyskiwanych produktów. Przede wszystkim kluczowe jest dokładne przygotowanie surowców – powinny one być odpowiednio oczyszczone i wolne od zanieczyszczeń, które mogłyby wpłynąć na wyniki destylacji. Ważne jest także monitorowanie parametrów operacyjnych takich jak temperatura i ciśnienie podczas całego procesu; ich stabilność ma istotny wpływ na efektywność separacji składników. Regularne czyszczenie aparatury również ma ogromne znaczenie – nagromadzone resztki substancji mogą prowadzić do obniżenia jakości produktów końcowych oraz zwiększenia ryzyka awarii sprzętu. Należy również zwrócić uwagę na dobór odpowiednich materiałów eksploatacyjnych oraz reagentów stosowanych w procesie; ich jakość powinna być zgodna z wymaganiami technologicznymi zakładu.
Jakie są przyszłe kierunki rozwoju technologii destylacji rozpuszczalników
Przyszłe kierunki rozwoju technologii destylacji rozpuszczalników będą koncentrować się głównie na zwiększeniu efektywności energetycznej oraz minimalizacji wpływu na środowisko naturalne. W miarę rosnącej świadomości ekologicznej przedsiębiorstw coraz większy nacisk kładzie się na wdrażanie technologii przyjaznych dla środowiska, takich jak odzysk ciepła czy zastosowanie odnawialnych źródeł energii w procesach przemysłowych. Równocześnie rozwijają się technologie membranowe oraz inne metody separacyjne, które mogą zastąpić tradycyjne metody destylacyjne w niektórych zastosowaniach dzięki swojej efektywności energetycznej i mniejszym kosztom operacyjnym. Ponadto rozwój sztucznej inteligencji i automatyzacji procesów przemysłowych otwiera nowe możliwości optymalizacji procesów destylacyjnych poprzez lepsze zarządzanie danymi i parametrami operacyjnymi w czasie rzeczywistym.