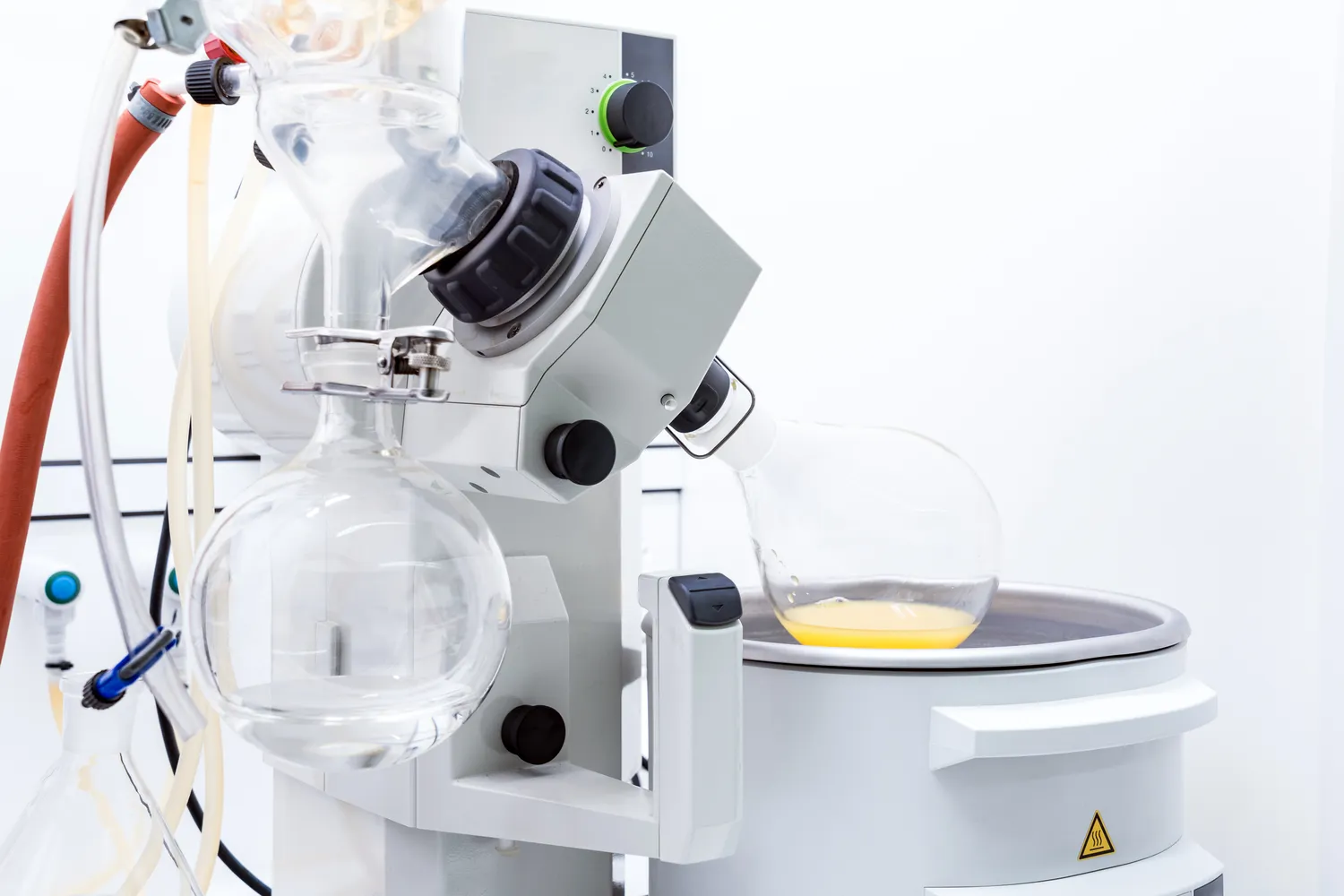
Destylarki do rozpuszczalników to urządzenia, które wykorzystują proces destylacji do oddzielania różnych substancji chemicznych na podstawie ich temperatury wrzenia. W praktyce oznacza to, że gdy mieszanka rozpuszczalników jest podgrzewana, substancje o niższej temperaturze wrzenia odparowują jako pierwsze, a następnie skraplają się w chłodnicy, tworząc czysty produkt. Ten proces jest niezwykle ważny w wielu dziedzinach, takich jak przemysł chemiczny, farmaceutyczny czy kosmetyczny. W przypadku destylacji prostych rozpuszczalników, takich jak etanol czy aceton, można osiągnąć wysoką czystość końcowego produktu. Warto również zauważyć, że istnieją różne typy destylarek, w tym destylarki prostego i frakcyjnego typu. Destylarki frakcyjne są bardziej skomplikowane i pozwalają na oddzielanie wielu składników z mieszanki jednocześnie, co czyni je idealnymi do bardziej złożonych procesów przemysłowych.
Jakie są zastosowania destylarek do rozpuszczalników
Destylarki do rozpuszczalników mają szerokie zastosowanie w różnych branżach przemysłowych oraz laboratoriach badawczych. W przemyśle chemicznym są one wykorzystywane do produkcji czystych substancji chemicznych, które są niezbędne do dalszej produkcji lub badań. Na przykład, w produkcji farb i lakierów destylacja pozwala na uzyskanie wysokiej jakości rozpuszczalników, które są kluczowe dla właściwości końcowych produktów. W laboratoriach naukowych destylarki są używane do oczyszczania reagentów oraz izolacji składników z mieszanin. Dzięki temu naukowcy mogą prowadzić dokładniejsze analizy i eksperymenty. Ponadto, w branży farmaceutycznej destylacja jest istotnym procesem przy produkcji leków oraz ich składników aktywnych. Umożliwia to uzyskanie substancji o wysokiej czystości, co jest kluczowe dla bezpieczeństwa i skuteczności leków.
Jakie są różnice między różnymi typami destylarek do rozpuszczalników
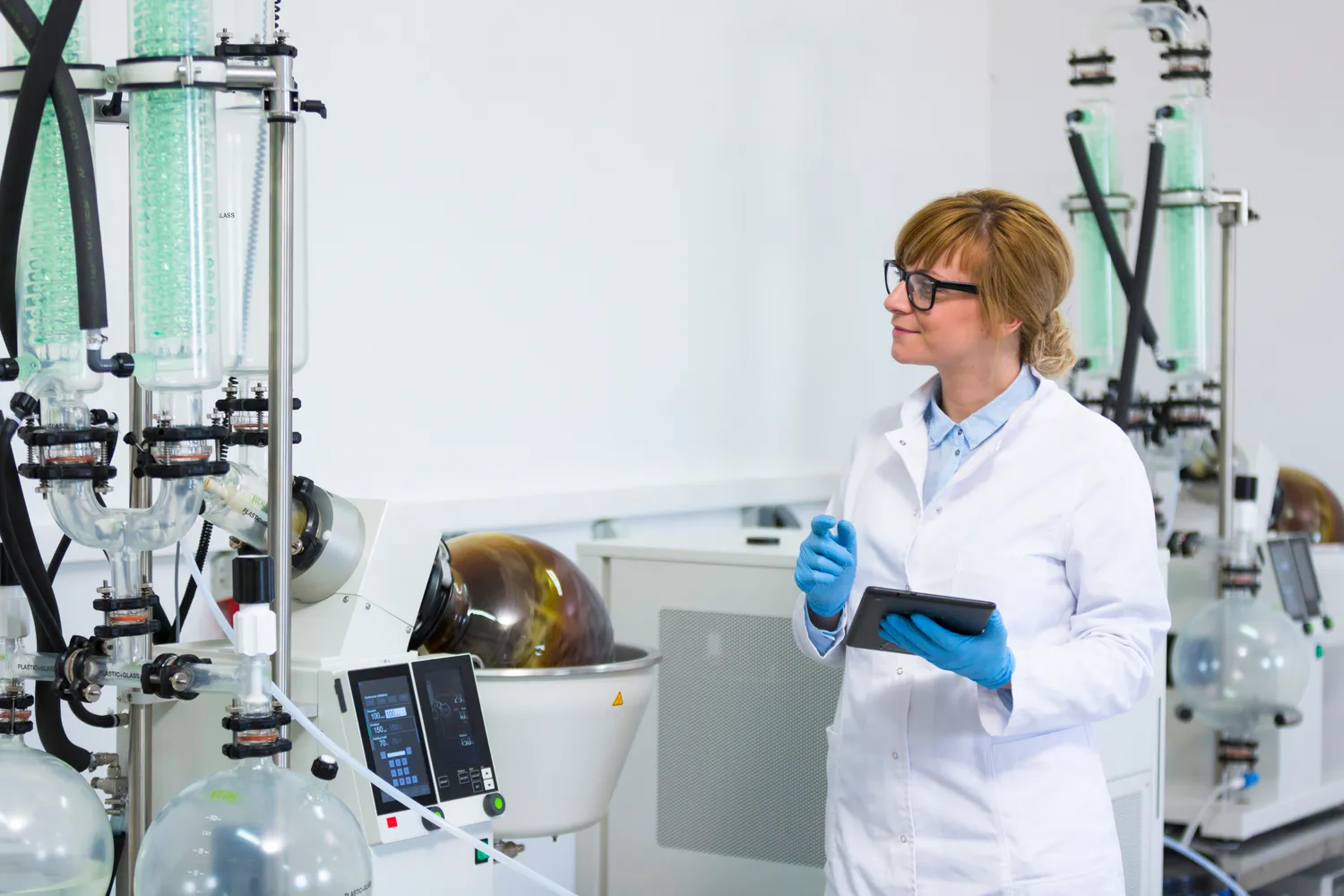
Wybór odpowiedniego typu destylarki do rozpuszczalników może być kluczowy dla efektywności procesu produkcyjnego. Istnieją różne rodzaje destylarek, które różnią się konstrukcją oraz przeznaczeniem. Najpopularniejsze z nich to destylarki proste i frakcyjne. Destylarka prosta składa się z podstawowych elementów: zbiornika na ciecz, źródła ciepła oraz chłodnicy. Jest ona idealna do separacji jednego składnika z mieszanki o wyraźnych różnicach temperatur wrzenia. Z kolei destylarka frakcyjna wyposażona jest w kolumnę frakcyjną, która pozwala na wielokrotne skraplanie i odparowywanie cieczy, co umożliwia oddzielanie kilku składników jednocześnie. Tego typu urządzenia są bardziej skomplikowane i droższe, ale oferują znacznie wyższą wydajność oraz czystość produktów końcowych.
Jakie czynniki wpływają na wybór destylarki do rozpuszczalników
Wybór odpowiedniej destylarki do rozpuszczalników powinien być oparty na kilku kluczowych czynnikach, które mogą znacząco wpłynąć na efektywność procesu oraz jakość uzyskanego produktu. Przede wszystkim należy zwrócić uwagę na rodzaj substancji, które będą poddawane destylacji. Różne substancje mają różne temperatury wrzenia oraz właściwości fizykochemiczne, co może wymagać zastosowania określonego typu urządzenia. Kolejnym istotnym czynnikiem jest skala produkcji – małe laboratoria mogą korzystać z prostszych modeli destylarek, podczas gdy duże zakłady przemysłowe będą potrzebować bardziej zaawansowanych systemów frakcyjnych lub rotacyjnych. Ważne jest również uwzględnienie kosztów eksploatacji oraz konserwacji urządzeń – niektóre modele mogą wymagać częstszej obsługi technicznej lub droższych materiałów eksploatacyjnych.
Jakie są najczęstsze problemy z destylarkami do rozpuszczalników
Podczas użytkowania destylarek do rozpuszczalników mogą wystąpić różne problemy, które mogą wpłynąć na efektywność procesu oraz jakość uzyskanego produktu. Jednym z najczęstszych problemów jest nieprawidłowe ustawienie temperatury, co może prowadzić do niepełnej destylacji lub przegrzewania substancji. W przypadku destylacji frakcyjnej, niewłaściwe ustawienia mogą skutkować mieszaniem się frakcji, co obniża czystość końcowego produktu. Kolejnym problemem jest osadzanie się zanieczyszczeń w kolumnach frakcyjnych, co może prowadzić do ich zatykania i obniżenia wydajności. Regularne czyszczenie i konserwacja urządzenia są kluczowe dla utrzymania jego sprawności. Inny istotny problem to wycieki cieczy, które mogą wystąpić w wyniku uszkodzeń uszczelek lub niewłaściwego montażu elementów. Wycieki nie tylko wpływają na bezpieczeństwo pracy, ale również mogą prowadzić do strat materiałowych. Warto również zwrócić uwagę na kwestie związane z chłodzeniem – niewystarczające chłodzenie może prowadzić do nieefektywnego skraplania pary, co obniża wydajność procesu.
Jakie są zalety korzystania z destylarek do rozpuszczalników
Korzystanie z destylarek do rozpuszczalników przynosi wiele korzyści zarówno w przemyśle, jak i w laboratoriach badawczych. Przede wszystkim, proces destylacji pozwala na uzyskanie wysokiej czystości substancji chemicznych, co jest niezwykle istotne w wielu zastosowaniach. Czyste rozpuszczalniki są kluczowe dla jakości produktów końcowych, zwłaszcza w branży farmaceutycznej i kosmetycznej, gdzie nawet najmniejsze zanieczyszczenia mogą wpłynąć na skuteczność leku lub kosmetyku. Kolejną zaletą jest możliwość odzyskiwania rozpuszczalników, co przyczynia się do zmniejszenia kosztów produkcji oraz ograniczenia negatywnego wpływu na środowisko. Dzięki destylacji można ponownie wykorzystać te same substancje w procesach produkcyjnych, co zmniejsza ilość odpadów chemicznych. Dodatkowo, nowoczesne destylarki często wyposażone są w zaawansowane systemy monitorowania i automatyzacji, co zwiększa komfort pracy oraz bezpieczeństwo użytkowników. Umożliwia to precyzyjne kontrolowanie parametrów procesu oraz szybką reakcję na ewentualne nieprawidłowości.
Jakie są najważniejsze cechy dobrych destylarek do rozpuszczalników
Wybierając odpowiednią destylarkę do rozpuszczalników, warto zwrócić uwagę na kilka kluczowych cech, które mogą znacząco wpłynąć na jej wydajność oraz funkcjonalność. Po pierwsze, istotna jest jakość materiałów użytych do konstrukcji urządzenia – stal nierdzewna czy szkło borokrzemowe to materiały odporne na działanie chemikaliów oraz wysokie temperatury. Po drugie, wydajność destylarki powinna być dostosowana do potrzeb użytkownika; im większa skala produkcji, tym bardziej zaawansowane urządzenie będzie potrzebne. Kolejnym ważnym aspektem jest łatwość obsługi i konserwacji – intuicyjny interfejs oraz dostępność części zamiennych mogą znacznie ułatwić codzienną pracę z urządzeniem. Dobrze zaprojektowana destylarka powinna również zapewniać wysoki poziom bezpieczeństwa pracy; systemy zabezpieczeń przed przegrzaniem czy wyciekiem cieczy są kluczowe dla ochrony użytkowników i środowiska. Warto również zwrócić uwagę na energooszczędność urządzenia – nowoczesne technologie pozwalają na zmniejszenie zużycia energii podczas procesu destylacji, co przekłada się na niższe koszty eksploatacji.
Jakie są trendy w technologii destylacji rozpuszczalników
W ostatnich latach technologia destylacji rozpuszczalników ewoluuje w kierunku coraz bardziej zaawansowanych i ekologicznych rozwiązań. Jednym z głównych trendów jest automatyzacja procesów destylacyjnych, która pozwala na precyzyjne kontrolowanie parametrów pracy urządzeń oraz minimalizację błędów ludzkich. Nowoczesne systemy monitorowania umożliwiają zbieranie danych w czasie rzeczywistym oraz ich analizę, co przyczynia się do optymalizacji procesów produkcyjnych. Innym istotnym trendem jest rozwój technologii próżniowej, która pozwala na obniżenie temperatury wrzenia substancji i tym samym zmniejszenie ryzyka degradacji termicznej cennych składników chemicznych. Próżniowe systemy destylacyjne stają się coraz bardziej popularne w branży farmaceutycznej oraz kosmetycznej ze względu na ich zdolność do uzyskiwania wysokiej czystości produktów przy zachowaniu ich właściwości biologicznych. Również rosnące zainteresowanie ekologicznymi rozwiązaniami sprawia, że producenci poszukują alternatywnych metod odzyskiwania rozpuszczalników oraz redukcji odpadów chemicznych.
Jakie są najlepsze praktyki dotyczące użytkowania destylarek do rozpuszczalników
Aby maksymalnie wykorzystać potencjał destylarek do rozpuszczalników oraz zapewnić ich długotrwałe i bezpieczne działanie, warto stosować kilka najlepszych praktyk dotyczących ich użytkowania. Po pierwsze, regularna konserwacja urządzeń jest kluczowa; należy dbać o czystość wszystkich elementów oraz kontrolować stan uszczelek i połączeń. Warto również przeprowadzać okresowe przeglądy techniczne zgodnie z zaleceniami producenta, aby uniknąć poważniejszych awarii w przyszłości. Kolejną ważną praktyką jest dokładne monitorowanie parametrów procesu podczas pracy – temperatura wrzenia czy ciśnienie powinny być regularnie kontrolowane i dostosowywane w razie potrzeby. Użytkownicy powinni także przestrzegać zasad bezpieczeństwa pracy; stosowanie odpowiednich środków ochrony osobistej oraz znajomość procedur awaryjnych to podstawowe wymagania dla osób obsługujących destylarki.
Jakie są różnice między domowymi a przemysłowymi destylarkami do rozpuszczalników
Destylarki do rozpuszczalników można podzielić na dwa główne typy: domowe i przemysłowe, które różnią się pod wieloma względami zarówno konstrukcją, jak i przeznaczeniem. Domowe destylarki zazwyczaj mają mniejsze rozmiary i prostszą konstrukcję; są one przeznaczone głównie dla hobbystów lub małych warsztatów zajmujących się produkcją alkoholu czy aromatów. Ich wydajność jest ograniczona i często nie spełniają rygorystycznych norm przemysłowych dotyczących czystości produktów końcowych. Z kolei przemysłowe destylarki charakteryzują się znacznie większą wydajnością oraz bardziej zaawansowaną technologią; często wyposażone są w systemy automatyzacji oraz monitorowania procesów produkcyjnych. Dzięki temu możliwe jest uzyskanie wysokiej czystości substancji chemicznych przy dużej skali produkcji. Ponadto przemysłowe modele często posiadają dodatkowe funkcje zabezpieczeń oraz systemy chłodzenia, które zwiększają bezpieczeństwo pracy i efektywność procesu.